Products
Production of ISNR involves a series of unit operations such as pre-cleaning, blending, final size reduction, drying and packing. The raw rubber in the form of latex and/ or Field Coagulam (FC) is converted into Blocks after pre-cleaning operations to remove foreign matter, washed, dried at a temperature not exceeding 110C, compressed into blocks of standard size and shape and wrapped in low density polythene film. Grading is done by taking samples from bales representing each lot and testing for dirt, ash, volatile matter, nitrogen content, initial plasticity and plasticity retention index. Block rubber is then packed in dispersible polythene. The weight of each bale is 25 Kg. Size of polythene used is 0.03+0.01 MM thick LDPE with melting point below 109 degree C.
Description
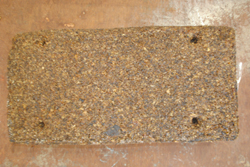
ISNR10:
Used for puncture patches for tyres, inner tubes cushion gums tocks, joint rings by injection moulding, raincoat proofing and packing, conveyor belts and footwear.
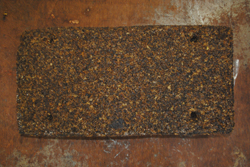
ISNR 20:
Used mostly for tyres & tubes, cushion gum stock, bicycle tyres-tubes, conveyor belts, footwear and other rubber goods.
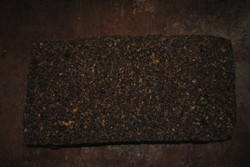
ISNR50:
Used for the production of less costlier non-critical applications like handmade hose, footwear, mats and moulded goods.
Characteristic |
ISNR 10 |
ISNR 20 |
ISNR 50 |
Dirt percent by mass (Max) |
0.10 |
0.20 |
0.50 |
Volatile matter, percent by mass (Max) |
0.80 |
0.80 |
0.80 |
Ash, percent by mass (Max) |
0.75 |
1.00 |
1.50 |
Nitrogen, percent by mass, Max |
>0.60 |
>0.60 |
>0.60 |
Initial plasticity Po (Min) |
30.00 |
30.00 |
30.00 |
Plasticity retention index, PRI |
50.00 |
40.00 |
30.00 |